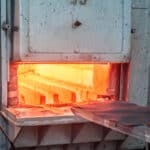
The Benefits of Metal Heat Treatment for Industrial Applications
January 28, 2025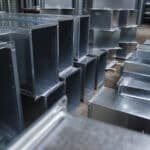
Vacuum Processing vs. Traditional Heat Treatment: What’s the Difference?
March 19, 2025Metal treating is a critical process in various industries, ensuring that metal components achieve the necessary strength, hardness, and durability for their applications. One of the most advanced techniques used in modern metallurgy is vacuum processing—a heat treatment method performed in a controlled, oxygen-free environment.
Vacuum processing offers several advantages over traditional heat treatment methods, including reduced contamination, improved mechanical properties, and precise control over metallurgical transformations.
What is Vacuum Processing in Metal Treating?
Vacuum processing is a specialized heat treatment technique conducted in a vacuum-sealed furnace. By removing atmospheric gases such as oxygen, nitrogen, and hydrogen, this process prevents oxidation, decarburization, and contamination that could weaken the metal.
Unlike conventional heat treatment methods that expose metals to air, vacuum processing creates a clean and controlled environment, allowing for precise heating, cooling, and transformation of metals at an atomic level. This technique is commonly used in industries such as aerospace, automotive, medical, and tool manufacturing, where metal integrity is crucial.
Why is Vacuum Processing Important?
Vacuum processing has become essential in modern metallurgy due to its ability to enhance metal properties while eliminating the drawbacks of conventional heat treatment. Here’s why it is widely used:
1. Prevents Oxidation and Surface Contamination
Metals treated in an oxygen-rich environment can develop scale, rust, and discoloration, which can negatively impact their performance. Vacuum processing eliminates this risk by creating an oxygen-free environment, resulting in a cleaner, corrosion-resistant surface.
2. Improves Mechanical Properties
By precisely controlling temperature and cooling rates, vacuum heat treatment enhances a metal’s strength, hardness, and durability. This is especially important for critical components used in high-stress applications such as aerospace turbines and medical implants.
3. Achieves Uniform Heating and Cooling
Traditional heat treatment can cause uneven heating, leading to distortions or microcracks in metal parts. Vacuum furnaces distribute heat evenly, reducing the likelihood of defects and ensuring dimensional stability.
4. Eliminates Decarburization
Decarburization is the loss of carbon from the metal surface due to exposure to oxygen at high temperatures. This can weaken the material and reduce wear resistance. Vacuum processing prevents carbon loss, maintaining the metal’s hardness and structural integrity.
5. Environmentally Friendly and Cost-Effective
Since vacuum processing doesn’t require toxic gases or excessive amounts of energy, it is a more sustainable and cost-efficient method compared to traditional heat treatments. Additionally, the lack of oxidation reduces the need for post-treatment cleaning or machining, lowering production costs.
How Does Vacuum Processing Work?
Vacuum processing involves several key steps to ensure the metal undergoes the necessary transformations while maintaining its structural integrity.
Step 1: Loading the Metal into the Vacuum Furnace
The metal parts to be treated are placed inside a specialized vacuum furnace, which is a sealed chamber capable of reaching high temperatures under low-pressure conditions.
Step 2: Evacuating the Furnace Chamber
A powerful vacuum pump removes all gases from the chamber, creating a near-perfect vacuum environment. This ensures that no contaminants interfere with the heat treatment process.
Step 3: Heating the Metal to the Desired Temperature
Once the chamber is vacuum-sealed, the furnace is heated to the required temperature (typically between 900°F and 2400°F, depending on the material and treatment process). The absence of oxygen prevents oxidation, allowing for clean, uniform heating.
Step 4: Holding at Peak Temperature
The metal is held at the peak temperature for a specific period to allow the desired metallurgical transformations to occur. This step is carefully controlled to ensure uniform material changes.
Step 5: Cooling (Quenching) the Metal
Once the heat treatment is complete, the metal is cooled at a controlled rate. Cooling may be performed using inert gases such as nitrogen or argon, depending on the desired hardness and microstructure. Rapid quenching can increase hardness, while slower cooling prevents internal stress buildup.
Step 6: Final Inspection and Quality Control
After processing, the treated metal undergoes quality inspection, including hardness testing, microstructural analysis, and dimensional checks to ensure it meets industry specifications.
Applications of Vacuum Processing in Different Industries
Vacuum processing is widely used in industries that require high-performance metals with superior mechanical and corrosion-resistant properties. Some common applications include:
1. Aerospace Industry
- Heat treatment of titanium and superalloys used in jet engines and structural components
- Improving fatigue resistance of landing gear and turbine blades
2. Automotive Industry
- Hardening of transmission gears, camshafts, and engine components
- Enhancing wear resistance of brake rotors and bearings
3. Medical Industry
- Sterile processing of surgical instruments and implants
- Strengthening stainless steel and titanium for medical devices
4. Tool and Die Manufacturing
- Hardening cutting tools, molds, and dies for prolonged durability
- Preventing cracking and distortion in precision machining tools
5. Energy Sector
- Enhancing the performance of nuclear reactor components
- Heat treating high-strength alloys used in wind and solar energy systems
Types of Vacuum Heat Treatments
Several vacuum heat treatment techniques are used depending on the application and material type. These include:
1. Vacuum Hardening
Involves heating metal above its critical transformation temperature and rapidly quenching it to achieve maximum hardness. Commonly used for tool steels and high-strength alloys.
2. Vacuum Annealing
A process where metal is heated and slowly cooled to relieve internal stresses and improve ductility. Ideal for stainless steel and aerospace alloys.
3. Vacuum Brazing
A high-precision joining method used to bond metal components with minimal distortion. Widely used in aerospace and medical device manufacturing.
4. Vacuum Carburizing
Introduces carbon into the surface of low-carbon steels under a vacuum environment to increase hardness and wear resistance.
Why Choose SWMT For Vacuum Processing?
Vacuum processing is a game-changer in metal treating, offering unmatched cleanliness, precision, and enhanced material properties. Whether in aerospace, automotive, or medical industries, this technique ensures that metals achieve superior performance while maintaining environmental and cost efficiency.
For manufacturers seeking high-quality, durable, and defect-free metal components, vacuum heat treatment is an essential process that guarantees reliability in demanding applications.
At Southwest Metal Treating, we specialize in advanced vacuum processing techniques tailored to meet industry standards. Contact us today to learn how our expertise can enhance the performance of your metal components.