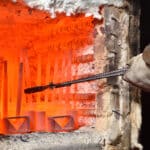
Comparing Different Metal Treating Techniques: Annealing, Quenching, Tempering & Carburizing
June 9, 2025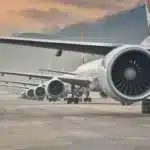
Why NADCAP Certification Matters for Aerospace Heat Treating
June 30, 2025In the metalworking and heat-treating industry, precision and performance are key. Whether you’re manufacturing aerospace parts, automotive components, or heavy machinery, the internal stresses in metal can significantly affect the final product’s strength, dimensional stability, and service life. This is where stress relieving plays a vital role.
Stress relieving is a heat treatment process that reduces residual stresses in metal materials without changing their overall mechanical properties. These residual stresses are often introduced during manufacturing processes such as welding, machining, cold working, and casting. If left untreated, they can cause distortion, cracking, and premature failure of the component.
At Southwest Metal Treating, stress relieving is one of our core services, ensuring your metal components maintain optimal integrity and performance throughout their lifecycle.
Why Stress Relieving Is Important
Residual stress may not always be visible to the naked eye, but its impact can be severe. Here’s why stress relieving matters:
1. Improves Dimensional Stability
When metal parts are subjected to further processing—such as machining or welding—residual stresses can cause them to shift or warp. Stress relieving minimizes these changes, preserving tight tolerances.
2. Reduces Risk of Cracking and Warping
Internal stresses can lead to cracking during service or subsequent heat treatments. By relieving these stresses, the risk of catastrophic failure is greatly reduced.
3. Enhances Performance and Longevity
Components that undergo stress relieving perform more reliably under operational loads, especially in high-temperature or high-stress environments.
4. Facilitates Further Processing
Stress-relieved parts are easier to machine and weld, helping reduce tool wear and improving precision in downstream operations.
What Causes Residual Stresses in Metals?
Residual stresses can be introduced during various metal-forming and processing methods, including:
- Welding: Intense heat and cooling cycles create differential expansion and contraction.
- Machining: High-speed cutting can produce thermal and mechanical stress near the surface.
- Cold Working: Rolling, bending, or drawing imparts strain into the material.
- Casting and Forging: Uneven cooling and solidification create internal tension.
- Heat Treatment: Hardening processes can induce stress unless controlled correctly.
How Stress Relieving Works
Stress relieving involves heating a metal to a specific temperature below its transformation point, holding it there for a predetermined time, and then slowly cooling it. This allows the internal stresses to redistribute and relax.
General Process Steps:
1. Heating
The part is uniformly heated in a controlled furnace to a temperature typically ranging from 900°F to 1,300°F (482°C to 704°C), depending on the material.
2. Soaking
The component is held at this temperature long enough to allow the internal stresses to relax. Soak time depends on the material and the thickness of the part—usually about 1 hour per inch of thickness.
3. Controlled Cooling
After soaking, the part is cooled slowly, either in the furnace or in still air, to avoid introducing new stresses through rapid temperature change.
Stress Relieving by Material Type
Different metals require different stress relieving temperatures and times:
- Carbon Steel: 1,100–1,250°F (593–677°C)
- Alloy Steel: 1,100–1,300°F (593–704°C)
- Stainless Steel: 900–1,050°F (482–566°C) to avoid sensitization
- Aluminum: Usually stress relieved through natural aging or controlled aging at low temperatures
- Cast Iron: Stress relieved around 1,000°F (538°C) to reduce hardening and cracking risks
Applications of Stress Relieving
Stress relieving is widely used across industries to improve reliability and quality of components, including:
- Aerospace components
- Automotive parts and frames
- Pressure vessels and piping
- Molds and dies
- Structural steel elements
- Machined parts and welded assemblies
Differences Between Stress Relieving and Other Heat Treatments
Heat Treatment | Purpose | Temperature Range | Alters Microstructure? |
Stress Relieving | Reduce residual stress | 900–1,300°F | No |
Annealing | Soften metal, improve ductility | 1,300–1,800°F | Yes |
Tempering | Reduce brittleness after hardening | 400–1,100°F | Yes |
Normalizing | Refine grain structure | ~1,600°F | Yes |
Stress relieving stands apart because it does not aim to change the hardness or structure of the material—only to reduce internal stress.
In-House vs. Commercial Stress Relieving
Some shops may attempt basic stress relieving in-house using welding preheat or post-weld heat, but precise control over temperature and atmosphere is crucial. Commercial heat treating facilities like Southwest Metal Treating offer advanced furnaces and certified procedures to ensure optimal results.
Key Considerations When Stress Relieving
When deciding on a stress relieving treatment, here are some important factors:
- Material type and thickness
- History of the component (e.g., cold worked, welded)
- Required mechanical properties
- Dimensional tolerances
- Downstream processing (machining, coating, etc.)
Providing this information to your heat-treating partner helps ensure a tailored, effective process.
Why Choose Southwest Metal Treating?
At Southwest Metal Treating, we bring decades of heat-treating expertise to every job. Our stress relieving services are:
- Precise: Controlled temperatures, accurate soak times, and uniform results.
- Scalable: From small parts to large weldments and fabrications.
- Certifiable: We adhere to industry standards, including AMS and ASTM specs.
- Responsive: Fast turnaround with attention to quality and service.
Whether you’re manufacturing aerospace parts or structural components, you can count on us to help your materials perform at their best.